In modern industrial and architectural fields, stainless steel serves as a crucial material, widely employed in various applications. The surface treatment methods directly influence the appearance, texture, and performance of stainless steel. This article provides an in-depth exploration of different surface treatment methods through a detailed chart, offering readers a deeper understanding and reference.
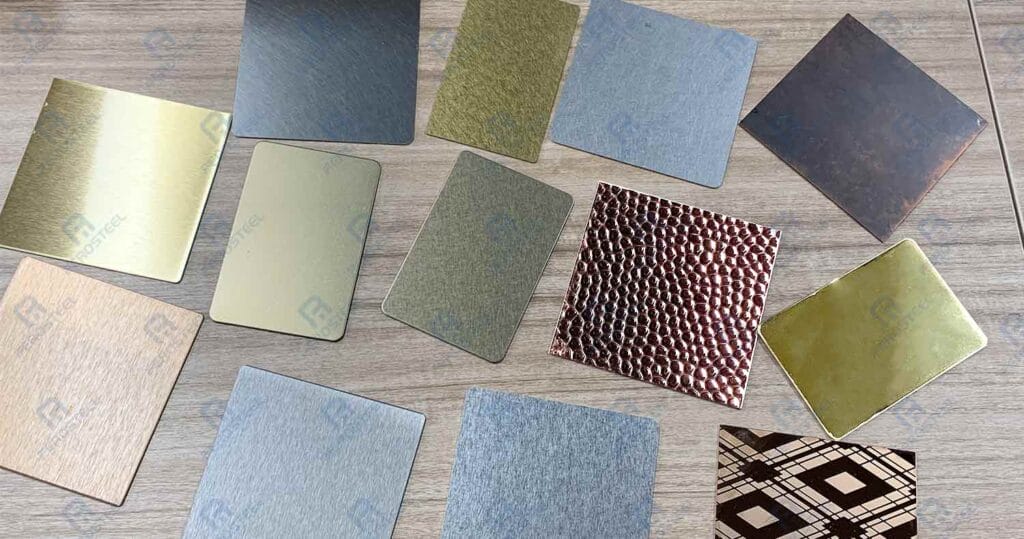
Stainless Steel Surface Treatment Chart
Surface Treatment Method | Description | Applications |
---|---|---|
Mirror Finish | Achieved through mechanical polishing and chemical treatments, providing high glossiness. | Architectural decoration, kitchen utensils, medical equipment, etc. |
Titanium Coating | Coating stainless steel with a layer of titanium film, imparting metallic texture and unique colors. | Interior decoration, furniture manufacturing, architectural facades, etc. |
Coating | Applying special coatings on stainless steel surface to achieve various colors and textures. | Artwork production, interior decoration, automotive components, etc. |
Sanding | Producing a delicate matte effect through mechanical grinding. | Elevator doors, wall decorations, kitchen equipment, etc. |
Sandblasting | Creating a uniform matte effect by blasting stainless steel surface with sand particles. | Flooring, handrails, outdoor decorations, etc. |
Stainless Steel Surface
Stainless steel surface refers to the outer layer or exterior of stainless steel material, which is renowned for its exceptional durability, corrosion resistance, and sleek appearance. The surface of stainless steel is typically smooth and shiny, thanks to its composition primarily consisting of iron, chromium, and other alloying elements. This composition forms a passive layer of chromium oxide on the surface, which acts as a protective barrier against corrosion and rust.
Stainless steel surfaces can be treated using various methods to achieve different textures, finishes, and appearances. These treatments may include polishing to create a mirror-like finish, sanding for a brushed or matte effect, or applying coatings for color and texture enhancements. Each treatment method offers unique aesthetic qualities and functional benefits, making stainless steel surfaces versatile and adaptable to a wide range of applications.
In architectural and interior design, stainless steel surfaces are often used for their modern and sophisticated look, making them popular choices for appliances, fixtures, and decorative elements. In industrial settings, stainless steel surfaces are valued for their hygienic properties and resistance to harsh chemicals, making them ideal for equipment and machinery in food processing, pharmaceuticals, and chemical processing industries.
Overall, stainless steel surfaces are prized for their combination of strength, longevity, and aesthetic appeal, making them a preferred material in various industries and applications worldwide.
Common stainless steel materials and their surface processing introduction
Overview of Commonly Used Surface Finishes for 201, 304, and 316L Stainless Steel
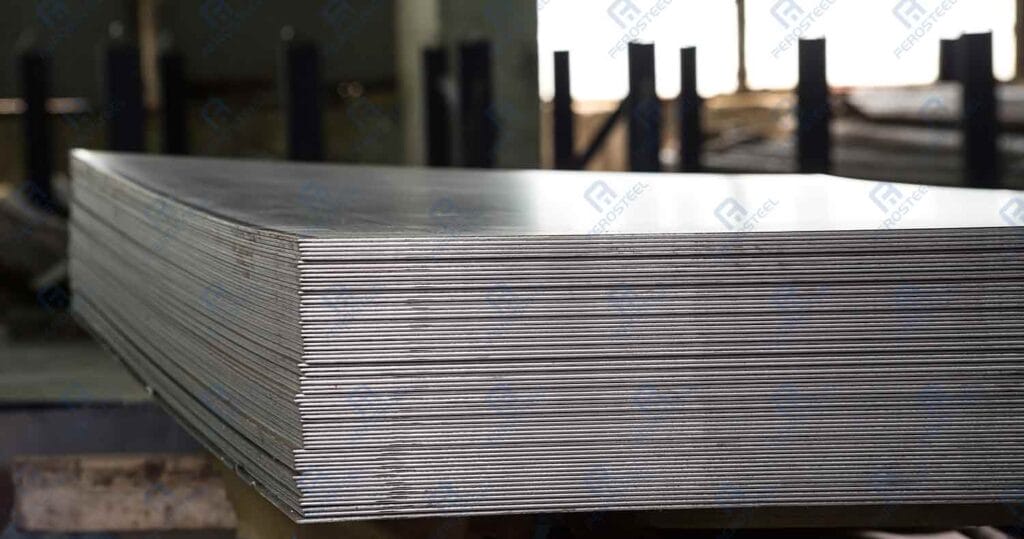
Stainless steel materials, including grades 201, 304, and 316L, are renowned for their durability, corrosion resistance, and versatility in various industries. Each grade offers unique properties suited for different applications, often complemented by specific surface finishes to enhance their performance and appearance.
Grade 201 stainless steel, known for its cost-effectiveness and practicality, commonly undergoes surface finishes such as mill finish, which is a standard industrial finish directly from the steel mill, providing a clean, smooth surface suitable for basic applications.
In contrast, grade 304 stainless steel, a widely used austenitic stainless steel, is favored for its excellent corrosion resistance and aesthetic appeal. Surface finishes for 304 stainless steel often include brushed or satin finishes, achieved through mechanical processes that create a uniform, matte appearance, ideal for architectural, decorative, and kitchen applications.
Grade 316L stainless steel, distinguished by its higher corrosion resistance and added molybdenum content, is preferred for more demanding environments, such as marine or chemical industries. Surface finishes for 316L stainless steel may include polished finishes, offering a reflective, mirror-like surface that enhances its resistance to corrosion and staining.
In summary, surface finishes play a crucial role in optimizing the performance and appearance of stainless steel materials. Understanding the surface finishes available for grades 201, 304, and 316L helps in selecting the most suitable option for specific applications, ensuring durability, aesthetics, and functionality.